Hybrid Timber Towers in Europe: Innovation in Prefabricated Multi‑Storey Design
- Kaspars Senvalds
- Apr 7
- 14 min read
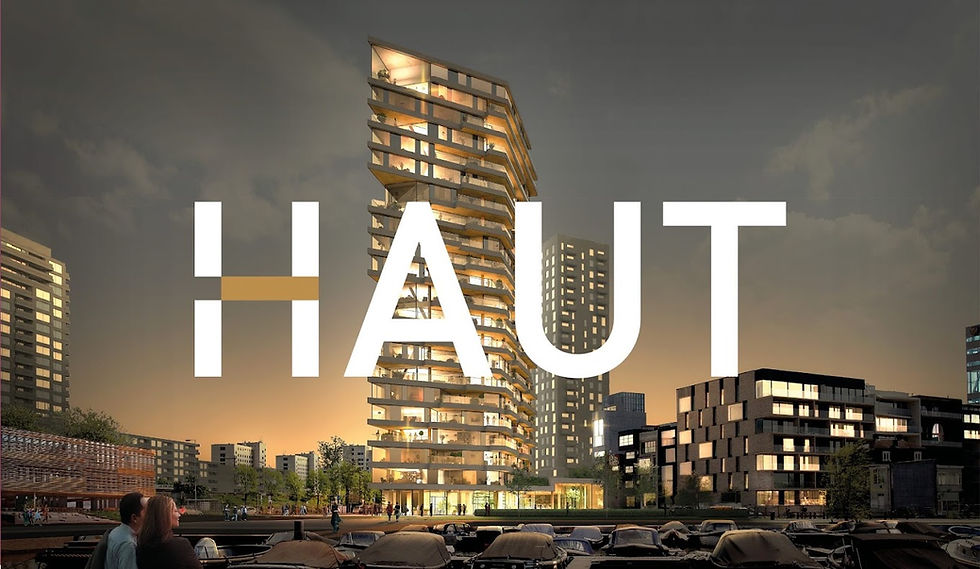
Modern engineered-wood buildings are pushing into high-rise territory across Europe. Architects and engineers are embracing mass timber – large-scale engineered wood like cross-laminated timber (CLT) and glulam – to build prefabricated multistory structures that are both sustainable and innovative. Yet building tall with wood comes with performance challenges. Designers must ensure that these lightweight, prefabricated wooden systems can match the safety and comfort of traditional concrete or steel buildings. Key concerns include:
Structural Integrity & Stability: Can a timber frame handle heavy loads and resist wind or seismic forces without excessive sway?
Fire Resistance: Will a wood building remain safe in a fire and meet strict European fire codes for multi-storey structures?
Acoustic Insulation: Can occupants enjoy quiet apartments, or will sound easily transmit through lighter wood floors and walls?
Vibration Control: Will occupants feel comfortable, without bouncy floors or perceptible building vibrations under wind or footfall?
European projects have shown these challenges are solvable. By leveraging hybrid construction – intelligently combining timber with steel and concrete – designers use each material to its strength. The result is a new generation of tall wood buildings that meet performance standards while delivering the benefits of sustainability and off-site prefabrication. Below, we explore each challenge and how hybrid timber design is overcoming it in practice.
Structural Integrity in Multi-Storey Timber Buildings
Structurally, timber is impressively strong relative to its weight, but it has a lower stiffness and mass than concrete or steel. This can make tall timber buildings more flexible. As building height increases, lateral loads from wind become a governing factor. Designers must control deflection and acceleration so that a timber tower doesn’t sway or vibrate uncomfortably under wind or seismic forces. In fact, studies confirm that above about 15–20 storeys, purely timber structures tend to be more sensitive to wind-induced vibrations than conventional high-rises, if not properly stiffened. Additionally, connections between prefabricated wood elements require special engineering to ensure robust load transfer at joints.
Hybrid structural systems are proving essential to ensure stability. A common approach is pairing a timber frame with a concrete or steel core for lateral stability. For example, the 84 m HoHo Tower in Vienna uses a solid concrete core (housing stairs and elevators) that stabilizes the building and provides a rigid spine for the timber structure. This concrete core doubles as a protected escape shaft in fire scenarios, simplifying approval from authorities. Around the core, the majority of the floors, beams, and columns are timber – in HoHo’s case, roughly 75% of the structure is wood. The concrete core and foundations carry lateral loads, while the timber elements handle vertical loads with much lower carbon footprint.

Beyond the core, engineers can introduce steel or concrete bracing elements in strategic locations. In some designs, steel moment frames or braced bays supplement a timber frame to resist wind or earthquakes. These stiffeners can often be left unwrapped (unprotected) if they are only required for rare extreme events. The overall hybrid strategy provides the needed stiffness and strength with minimal material. As one industry publication put it: “Beyond [~35 meters] height, a hybrid structure can provide additional stiffness; with a small amount of material the stability and horizontal stiffness can be improved” by adding steel or concrete where needed.
Equally important is the design of floors and diaphragms. Timber panels alone are lighter and flexible, but by creating timber-concrete composite (TCC) floors, engineers can achieve performance comparable to concrete slabs at a fraction of the weight. In a TCC floor, a thin concrete topping is bonded to a CLT or glulam panel, forming a composite that is stiffer and stronger than wood alone. This hybrid floor system was a focus of the landmark “LifeCycle Tower” research in Austria – the design criteria for its prefabricated wood-concrete slab were structural performance, fire protection and acoustic isolation, with careful attention to vibration as well. The concrete layer adds compression strength and stiffness, enabling longer spans and better load distribution. It also acts as a rigid diaphragm, improving the building’s overall lateral stability..
Thanks to these innovations, multi-storey timber structures once thought impractical are now feasible and safe. Advanced modeling and new wood products with improved engineering properties have made it possible to reach greater heights with wood.
Europe’s design codes (e.g. Eurocode 5) have provisions for engineered timber, and projects like the 21-storey HAUT in the Netherlands show that timber-hybrid high-rises can meet the same structural performance criteria as traditional construction. Engineers on HAUT used a concrete core and megacolumn, working in tandem with CLT floor panels, to satisfy the demanding deflection limits and stability requirements of a tall building.
The result is a sturdy structure that feels as solid as any conventional tower – but with a fraction of the foundation load, thanks to timber’s light weight. Lighter weight also brings seismic benefits: in earthquake-prone regions, timber’s low mass means lower inertia forces, reducing seismic demand on the structure. In short, hybrids take the best of each material – wood for light, sustainable load-bearing and steel/concrete for stiffness and robustness – to achieve structural integrity.
Fire Safety: Designing Combustible Materials to Meet Code
Fire resistance is perhaps the most critical challenge – and the most commonly cited concern – for multi-storey timber buildings. Historically, many European building codes placed strict height limits on wood structures (often 3–5 storeys) precisely due to fire safety worries.
The prospect of a high-rise with significant combustible material raises questions about how long the structure can withstand a fire and how to ensure safe evacuation. Public perception has also been a hurdle, as wood is intuitively seen as less fire-safe than concrete or steel.
In reality, mass timber can be engineered to achieve required fire ratings. Large timber members char on the outside at a predictable rate, forming an insulating char layer that protects the core. European standards (e.g. EN 1995-1-2) provide calculation methods for charring rates and reduced section properties, allowing engineers to size beams and panels so they will survive a 60 or 90-minute fire. For instance, the timber beams and CLT panels in the LifeCycle Tower system were designed to withstand REI 90 – 90 minutes of fire exposure – as confirmed by full-scale testing in Europe. This means they remain structurally intact for at least 1.5 hours of fire, giving time for occupants to evacuate and for sprinklers or firefighters to control the blaze.
Hybrid design greatly aids fire strategy. A common solution is using non-combustible elements (concrete or protected steel) to form natural fire barriers and safe zones. As noted, a concrete core not only provides stiffness but also acts as a 2-hour fire-rated stair/elevator shaft, protecting occupants during egress. Floor slabs can also serve as horizontal fire stops between levels. In modern timber towers, it’s typical to encapsulate wood elements with fire-rated boards (e.g. gypsum) or integrate concrete components such that flames are contained. For example, in a hybrid timber floor, the concrete topping itself can serve as a fire barrier for the wood underneath. Any exposed timber is carefully assessed – structural members can be oversized to allow for a sacrificial char layer while still supporting loads for the required duration. With these measures, timber buildings can meet the same fire code requirements as steel or concrete buildings. In fact, building codes in countries like Sweden, the UK, and France now accept mass timber construction for mid- and high-rise buildings, provided rigorous fire engineering is in place.
It’s worth noting that heavy timber can perform well in fire compared to unprotected steel. While steel may buckle when temperatures reach critical levels, a thick wood column will slowly char but often continue to carry load. This performance has been verified in tests and real fires. Nevertheless, conservative design is used: sprinklers are typically mandatory, and many designs use a “balanced design” approach (a mix of active fire suppression, passive fire resistance, and detection/alarm systems). The latest hybrid projects demonstrate that fire concerns, although valid, are addressable with engineering – and the industry is overcoming the perception issue through education and successful case studies. Each new project improves confidence that timber high-rises can be made just as fire-safe as any other building type.
Acoustics: Achieving Quiet Comfort in Wood Buildings
Another practical challenge in timber construction is acoustic performance – controlling sound transmission for quiet interiors. Wood is lighter and less dense than concrete, which means it doesn’t naturally block sound (especially low-frequency noise) as well as a heavy concrete structure. Without proper design, residents in a wooden apartment building might experience footsteps from above or voices through walls more readily than in a traditional building. Indeed, building acoustics has been a major focus of research in Europe’s push for taller wood buildings. Specialists have found that low-frequency sound (under ~100 Hz) is particularly troublesome in lightweight timber assemblies; traditional code tests haven’t always accounted for these frequencies, leading to designs that met regulations on paper but performed poorly in practice. Recent European projects like AkuLite and Silent Timber Build have worked to refine acoustic prediction models and criteria for wood structures, recognizing that excluding low-frequency vibration in design “optimizes [lightweight systems] completely wrong” and leaves them at a disadvantage versus heavy construction. In short, ensuring excellent sound insulation in multi-storey timber buildings is harder, but not impossible.
Hybrid construction again offers solutions. One advantage of adding concrete or steel components is increased mass and damping, which help dissipate sound energy. For example, timber-concrete composite floors significantly improve airborne sound insulation and reduce impact noise compared to all-wood floors. The concrete layer adds weight and stiffness, cutting down vibration transmission that would carry noise. In practice, many mass timber apartments use a concrete topping or a thick floating floor build-up (with insulation layers) over CLT panels to meet acoustic requirements. In the LifeCycle Tower prototype, the engineers incorporated a sound-absorbing raised floor and a self-leveling screed on the timber slabs to achieve the needed noise control – and the system met performance targets in testing. Walls and floor-ceiling assemblies are also detailed with isolating layers (resilient mounts, acoustic mats, etc.) to prevent direct sound paths through the wood structure.

European building regulations set strict sound insulation criteria for multi-family housing, and timber buildings now can fulfill them by design. For instance, the Wood Solutions Guide for Austria’s HoHo tower describes CLT floor assemblies with added acoustic insulation achieving the required ratings for airborne and impact sound. Decoupling is key: separating the layers (e.g. using suspended ceilings or floating floors) breaks the vibration paths. As a result of these innovations, it’s now routine for new timber residential buildings to include high-performance acoustic packages. Manufacturers of CLT and timber systems are well aware of what they must achieve, and solutions are continually improving. When done right, residents often can’t tell the difference – a timber-hybrid building can be as quiet as its concrete counterpart. Still, acoustics remains an area of active development, since achieving the same level of sound comfort often requires more complex assemblies in wood. The slight increase in complexity is a trade-off for the gains in sustainability and speed that timber provides.
Vibration and Comfort: Controlling Floor Bounce and Sway
Closely related to acoustics is the issue of vibration serviceability. Occupants of a building can feel vibrations from various sources: footfalls on a bouncy floor, or the whole building swaying slightly in the wind. Timber’s low mass and stiffness make it more prone to such vibrations if not carefully controlled. A thin CLT floor, for example, might deflect perceptibly under a person’s footstep, causing a “bouncy” feel. Likewise, a tall timber building that is too flexible could have a longer natural period and lower damping, potentially leading to noticeable motion at the top during strong winds. Human perception is very sensitive – even accelerations well below structural failure levels can cause discomfort – so engineers treat vibration performance as a critical design criterion.
Hybrid design greatly improves vibration performance. The composite floors mentioned earlier not only help acoustics but also increase floor stiffness and mass, thereby raising the natural frequency and damping of the floor system. Tests have shown that adding a concrete slab to a CLT panel floor can significantly reduce its vibration amplitudes and increase comfort levels. In one case study of a long-span CLT-concrete floor, the fundamental frequency and damping improved enough that the floor performed “reasonably well” under footfall, despite initial concerns. Essentially, the concrete acts to steady the timber floor, much like putting a heavy topper on a lightweight table to stop it from wobbling.
At the whole-building scale, materials can be combined to tune dynamic behavior. Interestingly, research indicates that a timber core can provide beneficial damping due to wood’s natural viscoelastic properties. For example, in the LifeCycle Tower analysis, a solid timber core had high damping and flexibility, which could absorb some sway, and when used in combination with a stiffer concrete core, the two systems could be tuned to damp out each other’s vibrations. Engineers can also integrate supplemental damping devices if needed (e.g. tuned mass dampers or viscoelastic braces), though in many mid-rise cases, hybrid structural measures alone suffice. The 18-storey Mjøstårnet tower in Norway – which held the title of world’s tallest timber building in 2019 – was designed with glulam trusses and bracing that keep accelerations within comfort limits, and its adjacent concrete structure (the podium and pool area) likely contributes additional damping mass. As a result, occupants can enjoy the views from a timber high-rise without sensing that it’s made of wood.

Design codes require that floor vibrations and lateral drift stay below thresholds (often governed by a 1/300 - 1/400 or similar span ratio for deflection and ISO comfort criteria for acceleration). Hybrid timber systems are engineered to meet these standards. In practice, this might mean using steel reinforcement or concrete ribs on a timber floor to stiffen it. It could also mean limiting bay sizes or adding columns to shorten spans. Because timber is so much lighter, sometimes additional weight is even added intentionally (for example, using a thicker concrete topping than structurally needed) purely to improve vibration performance. These measures, combined with analysis using finite element models and on-site testing, ensure that today’s multi-storey timber buildings achieve comfortable vibration serviceability. As one review summarized: well-engineered timber floors with a concrete layer can match the vibration and sound insulation properties of traditional floors, while cutting weight in half. In essence, hybrid construction lets us have the best of both worlds: a light, green building that still feels solid.
The Hybrid Advantage: Marrying Wood, Concrete, and Steel
What becomes clear is that hybrid structural design is the linchpin enabling taller timber buildings. Rather than building in wood alone, European projects increasingly use a mix of materials to meet all performance demands. Concrete and steel are used strategically – for example, concrete in the core and podium, steel connectors or braces for strength – while wood is used wherever possible for floor plates, beams, and columns. Each material addresses the other’s weaknesses: “This is where concrete comes into play – it is heavy, easy to install, cheap, and fireproof. Thus, all elements of [a tall timber building] are considered as hybrids.” By acting compositely, the hybrid system can achieve equal performance to an all-steel or all-concrete building, often at lower weight and with a significantly reduced carbon footprint.
Hybrid timber construction is also highly prefabricated. Engineered wood components are factory-built with precision, and even concrete parts (like cores or composite slabs) can be precast to fit. This dovetails with modern DFMA (Design for Manufacture and Assembly) practices. For example, the HoHo Vienna project stacked four types of prefabricated elements – timber columns, beams, floor panels, and facade panels – repeated across 24 floors. On site, assembly was rapid: only 1–2 weeks per floor because large modules arrived ready to bolt together. Timber’s high strength-to-weight ratio makes handling big panels easier, and there is less wet trade work, which speeds up construction. As Rune Abrahamsen, the engineer of Mjøstårnet, described, building in timber is “more or less like building Lego. You bring in large parts that you connect and install on site… you can assemble buildings very quickly.” The prefab approach improves quality control and reduces on-site waste as well – important aspects of sustainable construction.
Sustainability is a driving force behind these innovations. Wood is renewable and stores carbon, so increasing its use in place of cement and steel can significantly cut a building’s embodied CO₂. Hybrid timber buildings capitalize on this by maximizing the wood content without compromising on performance. The HAUT tower in Amsterdam, for instance, used over 2,000 m³ of timber, sequestering an estimated 1,800 tonnes of CO₂ in the structure, and achieved a 50% reduction in embodied carbon compared to a typical building. Yet it still meets all the functional demands of a modern high-rise – thanks to that concrete core and other hybrid elements ensuring safety and comfort. This balance of eco-friendliness and functionality makes hybrid timber design attractive not just as an engineering solution, but as a marketable product for developers and cities aiming for sustainability targets. It’s no surprise that cities like Amsterdam have set goals for a significant percentage of new buildings to use timber structure, or that multiple European countries are revising codes to facilitate taller wood buildings.
Finally, hybrid timber systems open new architectural possibilities. They allow the warmth and beauty of wood to be exposed in interiors, creating biophilic, appealing spaces, while still concealing fire protection layers and heavy elements where needed. Projects like the Sara Kulturhus in Sweden or the Brock Commons residence in Vancouver (though outside Europe) showcase elegant integrations of concrete cores with timber frames. In London, architects have used steel-timber composites in office buildings to achieve long spans with a distinctive aesthetic. These examples inspire confidence that hybrid timber construction is not a limitation but rather an opportunity for innovation. Each project serves as a learning laboratory, refining the techniques and proving the viability of prefabricated mass timber at greater scales.
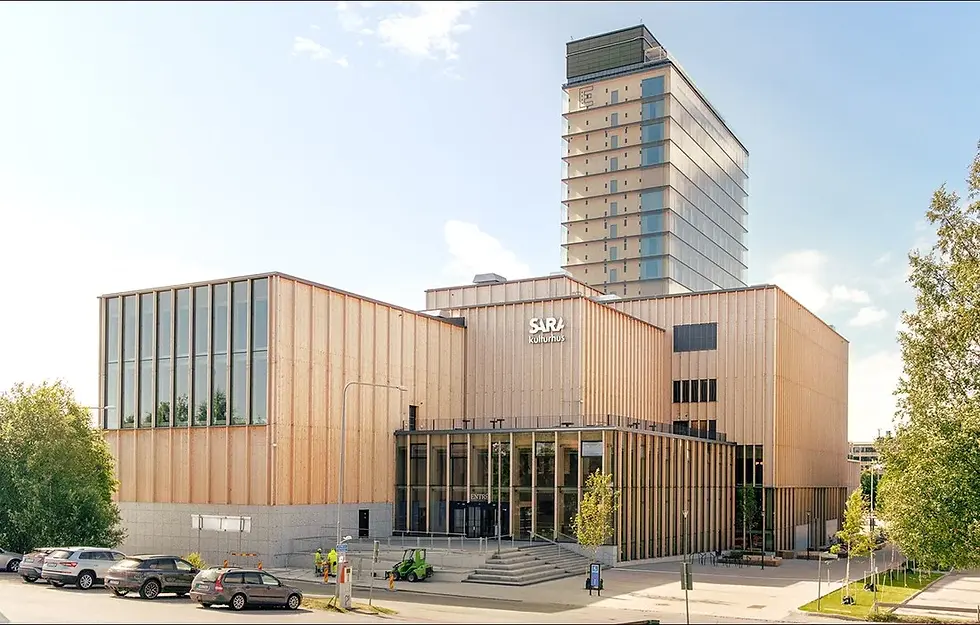
Conclusion: Building the Future with Hybrid Timber
Europe’s experience to date demonstrates that the engineering challenges of multi-storey timber construction – structural capacity, fire safety, acoustics, and vibration – can be successfully met through clever hybrid design. Ongoing research and pilot projects continue to improve knowledge, driving updates in standards and guidelines. The result is that what was once a niche experimental approach is rapidly becoming mainstream. Timber-hybrid buildings are rising in cities from Oslo to London, offering the twin benefits of sustainability and speed without sacrificing performance. By harnessing the complementary strengths of wood, concrete, and steel, architects and engineers have expanded the horizon of what timber can do.
The tone in the industry has shifted from “can we make it work?” to “look how well it works – and look at the advantages.” A new office or apartment tower can now be planned with prefabricated timber modules, knowing that with the right steel and concrete components in the mix, it will meet rigorous Eurocode standards and deliver a high-quality environment for occupants. Moreover, the innovative hybrid techniques developed for these projects are becoming exportable products themselves – design firms and contractors can apply the lessons to new projects around the world. As one case study concluded, a hybrid approach “enabled the team to overcome challenges related to fire safety, acoustics, and the structural demands of a high-rise” while drastically reducing carbon footprint. In short, hybrid prefabricated timber construction is turning challenges into triumphs.
For Europe’s architects and engineers, this is a thrilling development. It means the freedom to pursue bold, sustainable designs in wood without compromising on safety or comfort. Each successful multi-storey timber project – from pioneering towers like Mjøstårnet and HoHo to the many new proposals on the horizon – solidifies timber’s place in the future skyline. With innovation and careful engineering, wood is emerging as a true competitor to steel and concrete for urban construction, bringing us one step closer to cities that are as environmentally friendly as they are beautiful. The era of the hybrid timber skyscraper has only just begun, and its potential is sky-high.
References:
Abrahamsen, Rune. Euronews – “Get used to wooden skyscrapers...” (2018) – interview on tall timber advantages
Iqbal, Asif. “Developments in Tall Wood and Hybrid Buildings.” Sustainability Journal (2021) – on challenges and hybrid solutions
BREEAM Case Study: HAUT Amsterdam (2022) – details on hybrid design solving fire, acoustic, structural challenges
FPInnovations. “Timber-Concrete Composite Floors: a winning approach...” (2020) – on TCC floor benefits for acoustics and vibrations
CTBUH Journal (2014 Issue III). “Developing Hybrid Timber Construction for Tall Buildings.” – LCT project learnings on slabs and cores
Hagberg, K. & Bard, D. “Acoustics in Tall Wood Buildings – Challenges.” IoA Proceedings (2015) – low-frequency sound issue in lightweight construction
Lightwood report: “HoHo Vienna – World’s tallest timber building.” (2018) – hybrid concrete core and prefabrication details
Arup. Project Profile: HAUT, Netherlands’ Tallest Timber-Hybrid. (2022)
Comments